Description
The starting material for the production of cellulose ether is cellulose of hard wood, coniferous, or cotton (linters). Cellulose material is available in sheet, roll, or loose form, such as pre-cut cotton bales. The Precision Knife Mill, type PSN can grind each of these different types of cellulose. Conveyor belts are utilized to feed loose material and a metal detector prevents any metallic contamination. Cellulose sheets or rolls are fed into the grinding chamber via an integrated draw-in device. Fine cellulose powders produced distinguish themselves through high bulk density and improve the reaction and the fill weight in the reactor. The Precision Knife Mill has been specifically designed for the production of these powders. The upper part of the housing can be opened hydraulically thereby granting easy access to the grinding chamber for cleaning and maintenance.
Method of Operation
Rolls, sheets and strips are transported into the cutting chamber by means of profiled draw-in rollers. Precut material is fed via a feed chute. Size reduction to the desired end size is performed between the stator- and rotor knives in the housing. The end fineness is determined by various factors including the speed of the rotor and the type of screen insert. High-speed models with special rotors and screens are used for continuous grinding of sheet- and roll cellulose. The grinded end product is discharged straight down out of the cutting chamber, supported by suction and can be sacked underneath a cyclone or can be transported directly into a bin for further processing.
Schematic Layout
PULVERIZING CELLULOSE ROLLS
PULVERIZING of loose CELLULOSE FIBERS
Decisive advantages
- Production of fine powders with smooth surface and high viscosity
- Homogeneous end product with high bulk density
- Very good flowability
- Cool grinding by optimized air flow
- Fast and thorough cleaning due to easy access into the cutting chamber
- Easy screen and knife changing due to maintenance-friendly construction
- High economic efficiency and high throughput rate
- high number of 153 600 cuts per minute
- Easy infeed of the sheet-or roll cellulose
- After inserting the cellulose sheet, it is automatically wound off the roll and inserted into the mill by the draw-in device.
- Vibration-free installation of the mill and motor on the supporting frame
- Grinding at low temperature ensures a high quality powder
Applications
- Cellulose derivatives, such as MC, CMC, HEC, HPMC, MHEC etc, depending on the application, are contained as additives in many products in order to influence their characteristics.
- In the construction industry, they control the water binding ability of cement, gypsum and fillers.
- As additives in washing detergents, the derivatives prevent greying and discoloration.
- Cellulose derivatives, when used in foodstuffs, enhance composition, form, structure and consistency.
- The fine cellulose powders are used as fillers in the plastics- and rubber industry and are otherwise used in moulding compositions as a filter aid or as the basic material for the production of cellulose ether.
- Specifically In case of CMC, it is possibly the most well known product As wallpaper paste. In the pharmaceutical industry, CMC is used in tablets to define active ingredient release and as a binding agent.
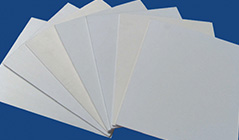
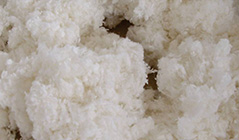